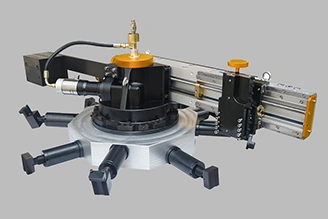
# Flange Facer Machine: Essential Tool for Pipeline Maintenance
## What is a Flange Facer Machine?
A flange facer machine is a specialized tool designed for resurfacing and repairing flange faces in pipeline systems. These machines play a critical role in maintaining the integrity of industrial piping networks by ensuring proper sealing surfaces between pipe flanges.
Flange facers are commonly used in oil and gas, petrochemical, power generation, and other industries where pipeline reliability is paramount. They help prevent leaks and maintain system pressure by creating perfectly flat and smooth flange surfaces.
## Key Features of Modern Flange Facers
Modern flange facer machines incorporate several important features:
– Portable design for on-site repairs
– Adjustable cutting tools for various flange sizes
– Precise alignment systems
– Multiple speed settings
– Durable construction for industrial environments
These features allow technicians to perform high-quality flange repairs without removing piping components from their installed positions.
## Types of Flange Facer Machines
There are several types of flange facers available:
### 1. Portable Flange Facers
These lightweight machines can be easily transported to job sites and mounted directly onto the flange for in-place machining.
### 2. Stationary Flange Facers
Larger, more powerful machines designed for shop use where flanges can be brought to the machine for resurfacing.
### 3. CNC Flange Facers
Computer-controlled machines offering the highest precision for critical applications.
## Applications in Pipeline Maintenance
Flange facer machines serve multiple purposes in pipeline maintenance:
– Repairing damaged flange faces
– Preparing new flanges for installation
– Resurfacing corroded or pitted flanges
– Creating special groove patterns for specific gasket types
– Maintaining sealing surfaces during pipeline modifications
## Benefits of Using Flange Facer Machines
The advantages of using professional flange facing equipment include:
– Reduced downtime compared to flange replacement
– Cost savings on new components
– Improved safety by ensuring proper sealing
– Extended service life of existing flanges
– Compliance with industry standards for surface finish
## Maintenance Tips for Flange Facer Machines
To ensure optimal performance and longevity of your flange facer:
– Regularly clean and lubricate moving parts
– Inspect cutting tools for wear and replace as needed
– Store the machine in a dry, protected environment
– Follow manufacturer’s guidelines for operation and maintenance
– Keep alignment components free from debris
## Choosing the Right Flange Facer
When selecting a flange facer machine, consider:
– The range of flange sizes you need to service
Keyword: flange facer machines
– Frequency of use
– Portability requirements
– Available power sources at job sites
– Budget constraints
Investing in quality flange facing equipment can significantly improve your pipeline maintenance capabilities and reduce long-term operating costs.