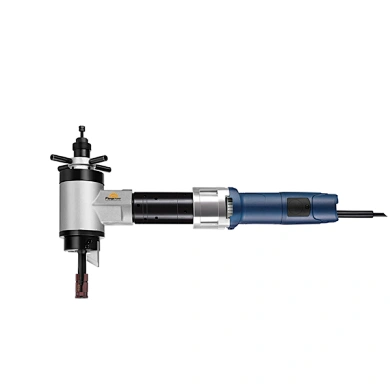
html
Portable Flange Facing Machine for On-Site Machining
In industrial maintenance and repair, the ability to perform precision machining on-site is invaluable. A portable flange facing machine provides the perfect solution for machining flanges without the need to disassemble and transport components to a workshop. This article explores the benefits, applications, and key features of these versatile machines.
What is a Portable Flange Facing Machine?
A portable flange facing machine is a compact, mobile unit designed to machine flange faces directly at the installation site. These machines can perform various operations including:
- Facing
- Grooving
- Boring
- Counterboring
- Spot facing
Key Advantages of On-Site Flange Machining
Using a portable flange facing machine offers numerous benefits for industrial operations:
1. Reduced Downtime
Eliminating the need to remove and transport components saves significant time compared to traditional machining methods.
2. Cost Savings
On-site machining reduces transportation costs and minimizes production losses from extended downtime.
3. Precision Results
Modern portable machines can achieve surface finishes and tolerances comparable to stationary machine tools.
4. Versatility
These machines can handle a wide range of flange sizes and materials, from carbon steel to high-grade alloys.
Typical Applications
Portable flange facers are used across multiple industries:
Keyword: portable flange facing machine
- Oil and gas pipelines
- Power generation plants
- Chemical processing facilities
- Shipbuilding and marine applications
- Water treatment plants
Choosing the Right Machine
When selecting a portable flange facing machine, consider these factors:
- Maximum flange diameter capacity
- Power requirements (electric, hydraulic, or pneumatic)
- Cutting tool compatibility
- Weight and portability features
- Available accessories and tooling
Investing in a quality portable flange facing machine can significantly improve maintenance efficiency and reduce operational costs for facilities that regularly work with flanged connections.